Can I make a table saw from a circular saw? Yes, you absolutely can! This guide provides a comprehensive walkthrough of how to perform a circular saw conversion to a DIY table saw, providing an affordable table saw alternative for woodworking enthusiasts. It will detail the tools, materials, and steps needed to construct a functional and safe homemade table saw.
Image Source: i.ytimg.com
Why Convert a Circular Saw into a Table Saw?
There are several compelling reasons to consider a circular saw table project. Here are a few key advantages:
- Cost Savings: A dedicated table saw can be a significant investment. Converting a circular saw is a much more affordable table saw build.
- Space Efficiency: If you have limited workshop space, combining tools is a great solution.
- Portability (Sometimes): While a full-sized table saw is stationary, smaller, DIY versions can be semi-portable.
- Versatility: A circular saw table saw modification can increase the functionality of your existing circular saw.
- DIY Satisfaction: There’s a great sense of accomplishment that comes from building your own tools.
Essential Tools and Materials
Before you begin, gather the necessary tools and materials. This list ensures a smooth and efficient building process.
Tools Required:
- Circular Saw: This is the heart of your project. Choose a corded model for consistent power.
- Drill/Driver: For assembling the table structure and mounting the saw.
- Jigsaw: For cutting intricate shapes in the tabletop, if needed.
- Measuring Tape: Accurate measurements are crucial for a functional table saw.
- Square: Ensures right angles for precise cuts.
- Safety Glasses: Protect your eyes from flying debris.
- Hearing Protection: Power tools can be loud.
- Clamps: Hold pieces securely during assembly.
- Screwdrivers: For tightening screws.
- Wrench Set: For tightening bolts.
- Router (Optional): For creating a smooth, flush surface around the saw plate.
Materials Needed:
- Plywood or MDF: For the tabletop and frame (¾ inch thickness is recommended).
- Lumber (2x4s): For constructing the table frame.
- Screws: For assembling the frame and tabletop.
- Bolts, Washers, and Nuts: For securing the circular saw to the table.
- Metal Plate (Optional): For a more robust saw mounting surface.
- On/Off Switch: Essential for safety. Choose a heavy-duty switch.
- Power Cord: If replacing the existing circular saw cord or wiring a separate switch.
- Wood Glue: Adds extra strength to joints.
- T-Track (Optional): For adding a miter gauge or other accessories.
- Fence Material: Wood or metal for creating a fence system.
Detailed Step-by-Step Instructions
Here’s a detailed guide on how to build your own table saw from a circular saw.
Step 1: Designing Your Table Saw
Before cutting any wood, plan your design. Consider these factors:
- Table Size: Determine the size of your tabletop based on your workspace and the size of materials you typically work with. A common size is 24 inches by 36 inches, but adjust to your needs.
- Saw Placement: Decide where the saw will be positioned within the table. Centering it provides balanced cutting capacity.
- Fence System: Plan for a fence system to guide your cuts. A simple fence can be made from straight lumber.
- Dust Collection (Optional): Consider incorporating a dust collection port for a cleaner workspace.
- Safety Features: Plan for a blade guard and a push stick to enhance safety.
Here is an example of a table size based on the size of the saw.
Circular Saw Blade Diameter | Recommended Table Top Size (Inches) |
---|---|
7 1/4″ | 24 x 36 |
6 1/2″ | 20 x 30 |
5 1/2″ | 18 x 24 |
Step 2: Building the Table Frame
- Cut the Frame Pieces: Cut the 2×4 lumber to the desired dimensions for your table frame. You’ll need four pieces for the perimeter and additional pieces for internal support.
- Assemble the Frame: Use screws and wood glue to assemble the frame. Ensure the corners are square using a square.
- Add Support: Add internal support pieces to the frame for added stability. These pieces should be evenly spaced and securely fastened.
Step 3: Creating the Tabletop
- Cut the Tabletop: Cut the plywood or MDF to the desired size.
- Mark the Saw Opening: Place the circular saw on the tabletop and trace the outline of the saw base. Accurately marking the opening is crucial for proper saw placement.
- Cut the Opening: Use a jigsaw to carefully cut out the opening for the circular saw. Ensure the opening is slightly larger than the saw base to allow for easy insertion and removal.
- Route the Edge (Optional): Use a router with a flush trim bit to create a smooth, flush surface around the saw plate. This step improves the accuracy and ease of use.
Step 4: Mounting the Circular Saw
This is a critical step that requires careful attention to detail.
- Prepare the Mounting Plate (Optional): A metal plate provides a more stable and durable mounting surface. Cut a piece of metal plate slightly larger than the saw base.
- Drill Mounting Holes: Place the circular saw on the mounting plate (or directly on the tabletop if not using a plate) and mark the mounting holes. Drill the holes to the appropriate size for your bolts.
- Attach the Saw: Use bolts, washers, and nuts to securely attach the circular saw to the mounting plate (or tabletop). Ensure the saw is level and firmly secured.
Safety Note: Double-check that the saw is securely mounted and cannot move during operation.
Step 5: Installing the On/Off Switch
Safety is paramount. Install a heavy-duty on/off switch within easy reach.
- Wire the Switch: Follow the manufacturer’s instructions to wire the switch to the circular saw’s power cord. If you’re not comfortable working with electricity, consult a qualified electrician.
- Mount the Switch: Mount the switch to the table frame in a convenient location.
Safety Note: Always disconnect the power cord before working on the electrical components.
Step 6: Building the Fence System
A fence is essential for making accurate and repeatable cuts.
- Cut the Fence Material: Cut the lumber or metal to the desired length for your fence.
- Create a Mounting System: Design a system to attach the fence to the table. This can be as simple as using clamps or building a more elaborate system with T-tracks.
- Ensure Accuracy: Ensure the fence is parallel to the saw blade for accurate cuts. Use a measuring tape to check the distance between the fence and the blade at multiple points.
Here is a comparison table of fence systems
Fence System Type | Complexity | Accuracy | Cost |
---|---|---|---|
Simple Clamp-On | Low | Medium | Low |
T-Track Based | Medium | High | Medium |
Micro-Adjustable | High | Very High | High |
Step 7: Adding Safety Features
- Blade Guard: Create a blade guard to protect your hands from the spinning blade. This can be made from clear acrylic or other durable material.
- Push Stick: Always use a push stick when cutting small pieces of wood. This keeps your hands away from the blade.
- Emergency Stop: Consider adding an emergency stop switch for quick shut-off in case of an emergency.
Safety Note: Never operate the table saw without these essential safety features.
Step 8: Testing and Adjustments
- Test the Saw: Before using the table saw for any serious projects, test it thoroughly. Make several test cuts to ensure the saw is cutting straight and the fence is accurate.
- Adjust as Needed: Make any necessary adjustments to the saw alignment, fence position, or blade height.
- Fine-Tune: Continuously fine-tune your table saw setup as you use it to achieve optimal performance.
Optimizing Your DIY Table Saw
Here are some ideas for improving the functionality and safety of your homemade table saw:
- Miter Gauge: Add a miter gauge for making accurate angled cuts.
- Dust Collection System: Connect a shop vacuum to a dust collection port to minimize dust and debris.
- Outfeed Support: Build an outfeed support table to support longer pieces of wood.
- Zero Clearance Insert: Create a zero clearance insert to reduce tear-out and improve cut quality.
Safety Precautions
Using a table saw, even a DIY version, requires strict adherence to safety guidelines.
- Always Wear Safety Glasses: Protect your eyes from flying debris.
- Use Hearing Protection: Table saws can be loud.
- Never Reach Over the Blade: Always use a push stick to keep your hands away from the blade.
- Keep Your Work Area Clean: A cluttered work area is a safety hazard.
- Never Force the Wood: Let the saw do the work. Forcing the wood can cause kickback.
- Disconnect Power When Adjusting: Always disconnect the power cord before making any adjustments.
- Inspect the Saw Regularly: Check for loose bolts, damaged blades, or other potential problems.
- Be Aware of Kickback: Kickback occurs when the wood is pinched between the blade and the fence, causing it to be violently thrown back towards the operator.
- Use Featherboards: Featherboards hold the wood firmly against the fence, preventing it from lifting or moving during the cut.
Troubleshooting Tips
- Saw Cuts Unevenly: Check the saw blade for sharpness and alignment.
- Fence is Not Parallel: Adjust the fence until it is parallel to the saw blade.
- Saw Vibrates Excessively: Ensure the saw is securely mounted and the blade is properly balanced.
- Motor Overheats: Check for proper ventilation and ensure the saw blade is not dull.
Alternative Table Saw Options
While building your own table saw is a rewarding project, there are also other affordable table saw options to consider:
- Jobsite Table Saws: These are portable and relatively inexpensive.
- Benchtop Table Saws: These are smaller and more affordable than full-sized table saws.
- Used Table Saws: Check online marketplaces or local classifieds for used table saws in good condition.
Frequently Asked Questions (FAQ)
-
What is the best type of circular saw to use for a table saw conversion?
A corded circular saw with a powerful motor is recommended for consistent performance. -
Can I use a cordless circular saw?
While possible, cordless saws may lack the sustained power needed for heavier tasks. -
Who should attempt this project?
Individuals with intermediate woodworking skills and a good understanding of power tool safety. -
How much does it cost to build a table saw from a circular saw?
The cost can vary depending on the materials you choose, but it typically ranges from $50 to $200. -
What are the safety risks involved?
The main risks include kickback, blade contact, and electrical shock. Always follow safety precautions. -
Is a DIY table saw as accurate as a professional table saw?
With careful construction and adjustments, a DIY table saw can be reasonably accurate, but it may not match the precision of a high-end professional model. -
Where can I find woodworking plans circular saw table project?
Online woodworking forums, websites, and YouTube channels offer various plans and tutorials. -
What is a zero clearance insert?
A zero clearance insert is a tabletop insert with a slot that closely matches the saw blade’s kerf, reducing tear-out and improving cut quality.
Converting a circular saw to a table saw is a rewarding and cost-effective project for any woodworking enthusiast. With careful planning, construction, and adherence to safety guidelines, you can create a functional and versatile tool for your workshop. This affordable table saw build will allow you to tackle a variety of woodworking projects with increased precision and efficiency. Remember to prioritize safety and take your time to ensure a successful outcome.
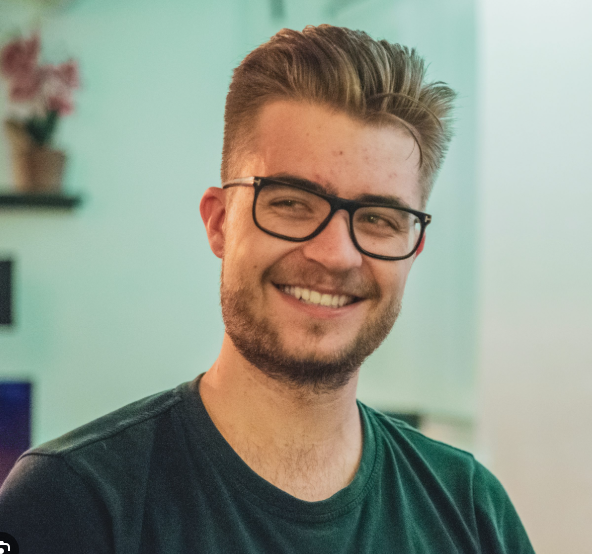
Hi, I’m Tom Scalisi, and welcome to The Saw Blog! I started this blog to share my hands-on experience and insights about woodworking tools—especially saws and saw blades. Over the years, I’ve had the chance to work with a wide range of tools, and I’m here to help both professionals and hobbyists make informed decisions when it comes to selecting and using their equipment. Whether you’re looking for in-depth reviews, tips, or just advice on how to get the best performance out of your tools, you’ll find it here. I’m excited to be part of your woodworking journey!