Can I make a table saw from a circular saw? Yes, you can absolutely build a DIY table saw from a circular saw. This circular saw conversion allows you to create a functional homemade table saw at a fraction of the cost of a professional model. This guide provides a detailed, step-by-step approach to build table saw from circular saw, including safety precautions and material considerations.
Image Source: i.ytimg.com
The Appeal of a DIY Table Saw
Why consider a circular saw table project instead of buying a ready-made table saw? Here’s why many woodworkers opt for this approach:
- Cost Savings: Building your own inexpensive table saw significantly reduces expenses compared to purchasing a new one.
- Customization: You can tailor the table saw to your specific needs and workspace.
- Skill Development: The project enhances your woodworking and problem-solving abilities.
- Recycling/Upcycling: Using a circular saw you already own is a great way to recycle tools.
Necessary Tools and Materials
Before beginning your circular saw modification, gather the following tools and materials. Quality is important for both safety and longevity.
Tools:
- Circular Saw: The heart of your new table saw. Choose a sturdy model with a powerful motor.
- Drill/Driver: For assembling the table and attaching components.
- Jigsaw or Circular Saw (for cutting the table top): Used to cut the large pieces of wood.
- Measuring Tape: For precise measurements.
- Square: To ensure accurate angles.
- Safety Glasses: Essential for eye protection.
- Hearing Protection: Protect your ears from loud noises.
- Clamps: To hold pieces together during assembly.
- Screwdrivers: Various sizes for different screws.
- Wrench Set: For tightening bolts and nuts.
- Router (Optional but Recommended): For creating smooth edges and grooves.
Materials:
- Plywood or MDF (for the table top and base): ¾ inch thickness is generally recommended.
- Lumber (for framing and support): 2x4s are commonly used.
- Screws: Various sizes for different applications.
- Bolts and Nuts: For securing the circular saw.
- Wood Glue: For strong and durable joints.
- T-Track (Optional): For adding accessories like miter gauges and featherboards.
- Switch: To control the power to the circular saw.
- Wiring and Electrical Connectors: For safe electrical connections.
- Blade Guard (Essential for safety): You can purchase or fabricate one.
- Rip Fence Materials (wood or metal): Helps with straight cuts.
Table 1: Material Cost Comparison
Item | DIY Cost (Approx.) | Pre-Built Table Saw Cost (Approx.) |
---|---|---|
Wood | $50 – $100 | N/A |
Hardware | $30 – $50 | N/A |
Circular Saw (if new) | $50 – $200 | Included in Saw Cost |
Table Saw | N/A | $200 – $1000+ |
Note: Costs are estimates and may vary based on location and material choices.
Step-by-Step Guide: Building Your DIY Table Saw
This guide outlines a general approach. Adapt the dimensions and design to your specific circular saw and desired table size.
Step 1: Designing the Table
Plan the table size according to your workshop space and the size of your circular saw. Consider the maximum cutting capacity you need. A table size of 24″ x 36″ is a common starting point. Sketch out your design, including the location of the circular saw and any accessories like a rip fence or miter slot.
- Considerations:
- Table Height: Should be comfortable for you to work at (typically around 36″).
- Saw Blade Exposure: Minimize the amount of blade exposed above the table.
- Dust Collection: Think about how you might incorporate dust collection.
Step 2: Constructing the Table Base
- Cut the Lumber: Cut the 2x4s to the required lengths for the frame.
- Assemble the Frame: Use screws and wood glue to assemble the frame. Ensure it is square.
- Add Support: Add cross braces to the frame for extra support and stability. These braces also provide a surface to mount the table top.
- Level the Base: Make sure the base is level. Use shims if necessary.
Step 3: Creating the Table Top
- Cut the Plywood/MDF: Cut the plywood or MDF to the desired size for the table top.
- Cut the Opening for the Circular Saw: Carefully measure and cut the opening for the circular saw. This is the most critical step for accurate cuts. Use a jigsaw for this, and make the hole slightly smaller than needed, then fine-tune with a router or file for a snug fit.
- Reinforce the Opening: Reinforce the edges of the opening with additional wood strips to prevent the plywood from splitting.
- Attach the Table Top to the Base: Securely attach the table top to the base using screws and wood glue.
Step 4: Mounting the Circular Saw
- Prepare the Mounting Brackets: Create brackets to hold the circular saw securely in place. These can be made from metal or wood.
- Attach the Brackets to the Saw: Attach the brackets to the circular saw, using existing screw holes if possible.
- Mount the Saw to the Table: Position the saw in the opening and attach the brackets to the table top. Ensure the blade is perpendicular to the table edge.
- Secure the Saw: Double-check that the saw is securely mounted and cannot move during operation.
Step 5: Adding the Power Switch
- Wire the Switch: Wire the power switch to the circular saw’s power cord. Follow all safety precautions and local electrical codes. If you’re not comfortable with electrical work, consult a qualified electrician.
- Mount the Switch: Mount the switch in a convenient location on the table.
- Test the Wiring: Before using the table saw, test the wiring to ensure it is working correctly and safely.
Step 6: Building a Rip Fence
A rip fence is essential for making accurate and repeatable parallel cuts. You can build a simple fence from wood or metal.
- Design the Fence: Design a fence that is easy to adjust and lock in place. Consider using a T-track system for added versatility.
- Build the Fence: Cut the materials to the required lengths and assemble the fence.
- Attach the Fence: Attach the fence to the table, ensuring it is parallel to the blade.
- Test the Fence: Test the fence to ensure it is accurate and easy to use.
Step 7: Adding a Blade Guard
A blade guard is crucial for safety. You can purchase a commercially made blade guard or fabricate one from clear plastic or metal.
- Mount the Guard: Mount the blade guard to the table, ensuring it covers the blade as much as possible.
- Test the Guard: Test the guard to ensure it does not interfere with the cutting process but provides adequate protection.
Step 8: Optional Features: Miter Slot and Featherboard
- Miter Slot: Cut a groove in the table top to accommodate a miter gauge. This allows for accurate angle cuts.
- Featherboard: Add a featherboard to hold the workpiece against the fence, improving accuracy and safety.
Safety Precautions
- Always wear safety glasses and hearing protection.
- Never operate the table saw without a blade guard.
- Use a push stick when cutting small pieces.
- Keep your hands away from the blade.
- Disconnect the power when making adjustments or changing the blade.
- Read and follow the manufacturer’s instructions for your circular saw.
- Make sure the blade is sharp and properly aligned.
- Never force the wood through the blade.
- Be aware of kickback and take steps to prevent it.
- Do not wear loose clothing or jewelry that could get caught in the blade.
Alternatives and Upgrades for your Homemade Table Saw
While the basic design covers the essentials, here are some upgrades and alternatives to consider as your woodworking skills develop or your needs change:
- Dust Collection System: Add a port to connect to a shop vacuum. This significantly reduces dust and improves visibility.
- Zero Clearance Insert: A zero-clearance insert reduces the gap around the blade, minimizing splintering and improving cut quality.
- Upgraded Fence System: Consider a more precise and adjustable fence system for greater accuracy.
- Outfeed Support: Add a folding outfeed table to support long workpieces.
- Mobile Base: Attach casters to the base to make the table saw easier to move around your shop.
Addressing Common Issues
- Vibration: Reduce vibration by using a sturdy base and ensuring all components are tightly secured.
- Accuracy: Calibrate the fence and blade to ensure accurate cuts. Use a precision square to check alignment.
- Power: If your circular saw lacks power, consider upgrading to a more powerful model or using a slower feed rate.
Table Saw Jig for Circular Saw
You can buy or make a table saw jig for circular saw. This is a more basic approach than building a full table. A jig lets you clamp your circular saw to a base and slide it along a rail for straight cuts. This is a simpler and cheaper alternative to a full table saw conversion, but offers less stability and functionality.
Is Building a DIY Table Saw Right For You?
Consider these points before starting your DIY table saw project:
- Your Skill Level: Are you comfortable with woodworking and basic electrical work?
- Your Budget: While cheaper than buying a table saw, there are still costs involved.
- Your Time: Building a table saw takes time and effort.
- Your Safety Concerns: Are you committed to following all safety precautions?
If you’re a reasonably skilled woodworker with a budget and a willingness to learn, building a DIY table saw can be a rewarding and cost-effective project. It is important to take the project seriously and ensure all work is completed to a high standard to ensure reliable and safe operation.
FAQ
Q: Is it safe to convert a circular saw to a table saw?
A: Yes, if done correctly and with strict adherence to safety precautions. A blade guard and push sticks are crucial.
Q: What size circular saw is best for a table saw conversion?
A: A 7 1/4 inch circular saw is a common and versatile choice.
Q: How much does it cost to build a table saw from a circular saw?
A: Typically between $100 and $300, depending on materials and the need to buy a circular saw.
Q: Can I use a cordless circular saw for this project?
A: While possible, a corded circular saw is generally preferred for consistent power.
Q: What is kickback, and how can I prevent it?
A: Kickback occurs when the blade catches the wood and throws it back towards the operator. Prevent it by using a sharp blade, a riving knife or splitter, and by never forcing the wood through the blade. Always stand to the side of the blade’s cutting path.
This comprehensive guide provides the information you need to convert circular saw to table saw successfully and safely. Enjoy your new woodworking projects with your homemade table saw!
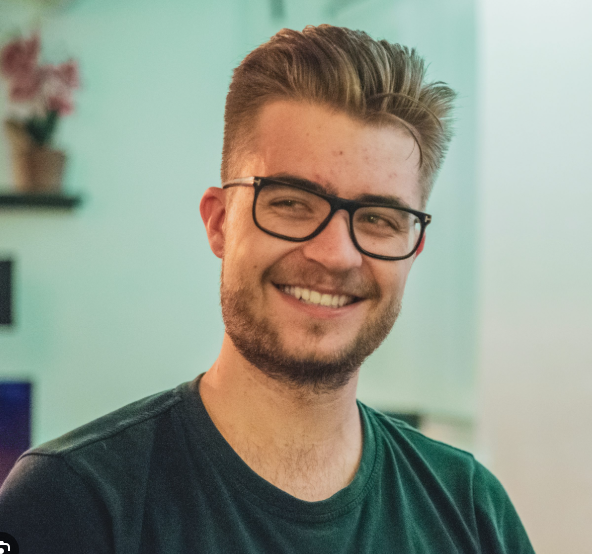
Hi, I’m Tom Scalisi, and welcome to The Saw Blog! I started this blog to share my hands-on experience and insights about woodworking tools—especially saws and saw blades. Over the years, I’ve had the chance to work with a wide range of tools, and I’m here to help both professionals and hobbyists make informed decisions when it comes to selecting and using their equipment. Whether you’re looking for in-depth reviews, tips, or just advice on how to get the best performance out of your tools, you’ll find it here. I’m excited to be part of your woodworking journey!