A table saw push stick is a crucial safety tool used to guide wood through the saw blade, keeping your hands away from the dangerous spinning blade. What is a table saw push stick? It’s a simple, often homemade, tool designed to apply pressure to the wood while maintaining a safe distance for your hands. This blog post will guide you through creating your own push sticks, exploring various designs, materials, and safe ripping techniques to enhance your woodworking experience and protect your fingers.
Image Source: i.ytimg.com
The Importance of Table Saw Safety Tools
Table saws are powerful tools that can be incredibly efficient, but they also pose a significant risk of injury. Using table saw safety tools, like push sticks, is not optional; it’s essential for protecting yourself.
Why Use a Push Stick?
- Keeps Hands Away from the Blade: This is the most obvious benefit. A push stick adds distance between your hand and the rotating blade.
- Maintains Consistent Pressure: Applying even pressure helps prevent kickback, a dangerous situation where the wood is thrown back towards the operator.
- Improves Accuracy: A firm and controlled grip on the workpiece leads to cleaner, more accurate cuts.
- Reduces Fatigue: Using a push stick allows you to apply pressure using your body weight instead of straining your hands and arms.
The Cost of Not Using Safety Tools
The consequences of neglecting table saw safety can be severe, including:
- Injuries: Cuts, lacerations, and even amputations are all possible outcomes of table saw accidents.
- Lost Time: Injuries can lead to missed work and significant recovery time.
- Financial Burden: Medical bills and lost income can create a substantial financial strain.
Fathoming Push Stick Design: Functionality and Ergonomics
What is a good woodworking push stick design? A good push stick design prioritizes safety, control, and comfort. There is no single “best” design, as the ideal push stick often depends on the specific task and user preference.
Key Elements of Effective Woodworking Push Stick Design
- Ergonomic Handle: A comfortable handle reduces hand fatigue and improves grip.
- Sturdy Construction: The push stick must be strong enough to withstand the force applied during cutting.
- Sufficient Length: The length should be appropriate for the type of cut being made, ensuring your hand stays a safe distance from the blade.
- Good Traction: The contact surface should provide a secure grip on the workpiece.
- Blade Guard Compatibility: The design should allow for easy use with the saw’s blade guard and other safety features.
Common Push Stick Designs
Here’s a comparison of some common push stick designs:
Design | Description | Pros | Cons | Best For |
---|---|---|---|---|
Standard Push Stick | A simple, flat piece of wood with a handle and a notch for pushing. | Easy to make, inexpensive. | Limited control, may not be suitable for thin or narrow pieces. | General purpose ripping of thicker stock. |
L-Shaped Push Stick | Shaped like an “L,” providing both downward and forward pressure. | Offers better control than the standard design, good for thin stock. | Can be more difficult to maneuver, may not be suitable for all cutting scenarios. | Ripping thin stock, edging, and situations requiring greater control. |
Gripper Push Stick | Features a rubber or high-friction material on the bottom for extra grip. | Provides excellent control, reduces the risk of slipping. | May be more expensive to make, requires specialized materials. | Ripping small pieces or when extra grip is needed. |
Long Reach Push Stick | Extended length to be used for ripping full length boards. | Good for providing control and pressure from afar. | Requires more material, can be cumbersome if you don’t have space. | Long board ripping with limited fence contact. |
Push Block | Uses handles to provide downward pressure, not good for pushing full pieces | Good for applying a lot of downward pressure and cutting small pieces of wood safely. | Not good for ripping full pieces of wood, not a substitution for a push stick. | Providing downward pressure when routing or cutting small pieces on the table saw safely. |
Ergonomic Considerations for Push Stick Design
Creating an ergonomic push stick means designing it to fit your hand and working style.
- Handle Shape and Size: Experiment with different handle shapes and sizes to find what feels most comfortable and secure. Consider the size of your hands when making a push stick.
- Grip Material: Using a non-slip grip material, such as rubber or textured paint, can improve control and reduce hand fatigue.
- Weight and Balance: A well-balanced push stick will be easier to control and less tiring to use.
Shop-Made Push Stick Tutorial: A Step-by-Step Guide
Looking for a shop-made push stick tutorial? This section provides a detailed guide to building a simple, effective push stick using common materials and tools. This DIY push stick plan will help you create a safe and reliable tool for your table saw.
Materials Needed
- 3/4″ Plywood or Hardwood (Approximately 6″ x 12″)
- Wood Glue
- Screws (1 1/4″ or similar)
- Sandpaper (120-grit and 220-grit)
- Non-slip material (optional)
Tools Needed
- Table Saw
- Drill
- Screwdriver
- Clamps
- Measuring Tape or Ruler
- Pencil
- Safety Glasses
- Hearing Protection
Step-by-Step Instructions
- Prepare the Wood: Cut the plywood or hardwood to the dimensions of 6″ x 12″. Sand the edges and surfaces smooth.
- Cut the Handle: On one end of the board, mark out a handle shape. A simple curved handle works well. You can use a jigsaw or bandsaw to cut out the handle. Alternatively, you can cut it out on the table saw slowly and carefully.
- Create the Push Notch: On the opposite end of the handle, cut a notch that will grip the edge of the workpiece. This notch should be about 1″ deep and 1/2″ wide. You can create this notch using the table saw, making multiple passes to widen the cut.
- Add Reinforcement (Optional): To increase the strength of the push stick, consider adding a second layer of wood to the handle area. Glue and screw this second piece in place.
- Sand and Finish: Sand the entire push stick smooth, paying particular attention to the edges and handle. Apply a finish if desired, such as a clear coat or varnish.
- Add Non-Slip Material (Optional): If you want to improve the grip of the push stick, apply non-slip material to the bottom surface. This could be rubber, sandpaper, or a specialized non-slip coating.
Table: Materials Costs Comparison
Material | Estimated Cost |
---|---|
3/4″ Plywood | \$5 – \$10 |
Hardwood Scrap | \$5 – \$15 |
Wood Glue | \$5 |
Screws | \$3 |
Sandpaper | \$3 |
Non-slip Material | \$5 – \$10 |
Total Estimated Cost | \$26 – \$51 |
Safe Ripping Techniques: Integrating the Push Stick
How do I use a push stick to safely rip lumber on a table saw? Mastering safe ripping techniques is crucial for using a table saw effectively and minimizing the risk of injury. The push stick is a key component of these techniques.
Essential Table Saw Safety Tips
- Read the Manual: Familiarize yourself with your table saw’s operating instructions and safety guidelines.
- Wear Safety Gear: Always wear safety glasses and hearing protection when using a table saw. A dust mask or respirator is also recommended.
- Inspect the Saw: Before each use, inspect the saw for any damage or loose parts. Ensure the blade is sharp and properly aligned.
- Use a Sharp Blade: A dull blade is more likely to cause kickback.
- Stand to the Side: Never stand directly behind the saw blade. Stand to the side to avoid being hit by kickback.
- Use a Featherboard: Featherboards hold the workpiece firmly against the fence, improving accuracy and reducing the risk of kickback.
- Never Reach Over the Blade: If you need to adjust the workpiece, turn off the saw and wait for the blade to stop spinning.
- Don’t Force the Cut: Let the saw do the work. Forcing the cut can lead to kickback or other dangerous situations.
Using the Push Stick for Ripping
- Position the Workpiece: Place the workpiece against the fence and ensure it is flat on the table.
- Start the Cut: Turn on the saw and slowly feed the workpiece into the blade, using your hands to guide it initially.
- Engage the Push Stick: Once your hands are within about 6 inches of the blade, use the push stick to continue pushing the workpiece through the cut.
- Apply Even Pressure: Maintain consistent pressure on the workpiece, both downward and forward.
- Complete the Cut: Continue pushing the workpiece through the blade until the cut is complete.
- Turn Off the Saw: Turn off the saw and wait for the blade to stop spinning before removing the cut piece.
Best Practices for Specific Scenarios
- Ripping Thin Stock: When ripping thin stock, use an L-shaped push stick or a push block to maintain better control.
- Ripping Wide Stock: For wide stock, use a featherboard to keep the workpiece firmly against the fence.
- Dealing with Kickback: If you experience kickback, immediately turn off the saw and step away. Do not try to catch the workpiece.
Push Block Alternatives: Expanding Your Safety Arsenal
What are some effective push block alternatives, or are they needed in addition to a push stick? While the push stick is a versatile tool, push blocks offer additional safety and control in certain situations, particularly when working with small pieces or needing more downward pressure.
Push Block Designs and Uses
- Handle Push Block: A simple block with a handle on top. Provides downward pressure and control.
- Heel Push Block: Features a “heel” that hooks over the back edge of the workpiece. Prevents the workpiece from lifting during the cut.
- Multi-Purpose Push Block: Combines features of both handle and heel push blocks.
When to Use a Push Block
- Small Pieces: Push blocks are ideal for cutting small pieces of wood, as they provide a secure grip and keep your fingers away from the blade.
- Routinely on thin material: Using a push stick on thin material can be difficult, push blocks keep your hands safely away from the blade.
- Shaping: Use a push block when cutting shapes.
- Applying Downward Pressure: Push blocks excel at applying downward pressure, which is important for preventing the workpiece from lifting during the cut.
- Routing Operations: Push blocks can also be used during routing operations on a router table.
Building a Push Stick Jig: Enhancing Precision and Safety
Can I build a push stick jig to enhance table saw safety? Yes, building a push stick jig can significantly improve the precision and safety of your table saw cuts, particularly for repetitive tasks.
Types of Push Stick Jigs
- Tapering Jig: Allows you to cut tapered pieces of wood safely and accurately.
- Miter Jig: Helps you make precise miter cuts on the table saw.
- Dado Jig: Simplifies the process of cutting dadoes and grooves.
Benefits of Using a Push Stick Jig
- Improved Accuracy: Jigs provide a stable platform for the workpiece, leading to more accurate cuts.
- Increased Safety: Jigs keep your hands further away from the blade and reduce the risk of kickback.
- Repeatability: Jigs allow you to make the same cut repeatedly with consistent results.
- Efficiency: Jigs can speed up the cutting process, especially for repetitive tasks.
Frequently Asked Questions (FAQ)
Q: What type of wood is best for making a push stick?
A: Hardwoods like maple, oak, or birch are ideal for push sticks due to their strength and durability. Plywood is also a good option, especially Baltic birch plywood. Avoid using softwoods like pine, as they can be too soft and prone to splintering.
Q: How often should I replace my push stick?
A: Inspect your push stick regularly for wear and tear. Replace it if it becomes damaged, worn, or develops splinters.
Q: Can I use a push stick on a miter saw?
A: While push sticks are primarily designed for table saws, smaller push blocks are safe to use on miter saws.
Q: Is it safe to use my hands instead of a push stick?
A: No. It is never safe to use your hands instead of a push stick when operating a table saw. Push sticks are designed to keep your hands a safe distance from the blade, preventing serious injuries.
Q: Where can I find DIY push stick plans online?
A: Many websites and woodworking forums offer free DIY push stick plans. A simple search for “DIY push stick plans” or “homemade table saw accessories” will turn up numerous options.
By taking the time to craft your own push sticks and integrating them into your safe ripping techniques, you’ll be taking a significant step toward enjoying woodworking while prioritizing safety. A well-made push stick is an inexpensive investment that can pay dividends in peace of mind and protection from injury.
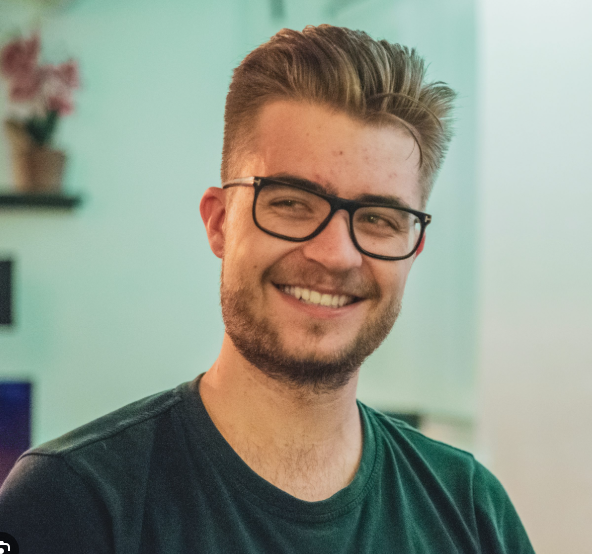
Hi, I’m Tom Scalisi, and welcome to The Saw Blog! I started this blog to share my hands-on experience and insights about woodworking tools—especially saws and saw blades. Over the years, I’ve had the chance to work with a wide range of tools, and I’m here to help both professionals and hobbyists make informed decisions when it comes to selecting and using their equipment. Whether you’re looking for in-depth reviews, tips, or just advice on how to get the best performance out of your tools, you’ll find it here. I’m excited to be part of your woodworking journey!